
Navigating Change in Manufacturing
Enhance productivity, reduce burnout, and retain skilled talent with customized training and wellness solutions designed specifically for manufacturing teams
Industry Challenges
The manufacturing industry is undergoing significant transformation, driven by automation, digitization, and the demands of a new generation of workers. From adapting to advanced technologies to attracting and retaining young talent, manufacturers must prioritize employee development and operational efficiency to stay competitive.. Here’s a closer look at these challenges—and the hidden costs of not addressing them:
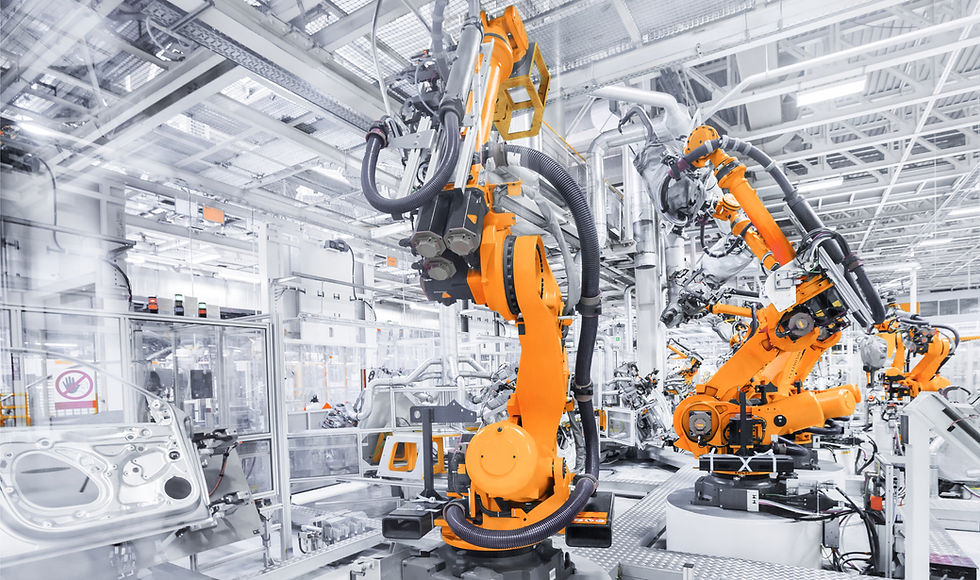
1
Attracting Talent
Younger workers prioritize career development, meaningful work, and mental health support, making traditional manufacturing workplaces less appealing. High turnover and low engagement hinder productivity and increase costs.
-
Cost Impact: Recruitment and training costs can range from $5K–$20K per employee. Frequent turnover leads to additional inefficiencies and expenses.
-
Time Impact: Hiring and onboarding replacements take 4–8 weeks, creating operational delays.
2
Adjusting to
Digital Tools
Industry 4.0 technologies require employees to gain technical skills to operate and maintain advanced equipment. Skills gaps slow the adoption of automation and reduce productivity.
-
Cost Impact: Downtime caused by undertrained staff can cost manufacturers $10K–$50K per hour, depending on the scale of operations.
-
Time Impact: Training employees on new tools without structured programs can take several weeks to months, delaying full implementation.
3
Reducing Injuries & Burnout
Physically demanding tasks and high-pressure environments in manufacturing often lead to injuries and burnout, driving absenteeism, turnover, and increased costs.
-
Cost Impact: Workplace injuries cost $40K–$100K per claim, while burnout-related absenteeism and turnover add $1,500–$3,000 per employee.
-
Time Impact: Injuries and burnout result in lost workdays, disrupted schedules, and time spent training replacements.
How ESM Helps
We design custom onboarding and wellness programs, including stress management, leadership training, and career progression. Our approach improves engagement, reduces turnover, and saves businesses $10K–$50K.
How ESM Helps
We provide tailored training programs focused on upskilling employees in automation and digital tools, ensuring a smoother transition to Industry 4.0. This minimizes downtime and accelerates productivity.
How ESM Helps
Our programs provide proactive strengthening and injury prevention training, and stress management workshops to reduce strain, prevent injuries, and improve morale, saving $50K–$200K.
Client Success Story
Muskoka Brewery, a leading Canadian brewery recognized for its award-winning handcrafted beers and spirits, partnered with ESM to enhance employee performance and well-being. As a Great Place to Work and Living Wage Certified Brewery, the company was committed to maintaining a positive workplace culture. However, they faced increasing challenges related to work demands, work-life balance, and employee health concerns, impacting engagement, productivity, and overall workplace satisfaction.
"ESM provides concrete data that highlights both our strengths and areas for growth, giving us clear opportunities for improvement. Their trustworthy resources empower employees, managers, and leaders alike, complementing our existing programs while fostering teamwork through shared tools and strategies."
- HR & People Manager, Muskoka Brewery
Our Approach
1. Performance Pulses to Identify Key Challenges
We conducted bi-monthly Performance Pulses to assess risks affecting employee well-being and performance across all departments. This data provided leadership with clear insights into workforce stressors, helping them make informed decisions about employee support and development.
2. Tailored Training for Support Employee Resilience
We designed customized performance training to help employees manage workplace disruptions, build stress resilience, and sustain productivity. By focusing on managing change, improving mental fitness with neuroscience, and enhancing frontline performance, we equipped both brewery and remote employees with practical strategies to balance workloads, reduce burnout, and stay engaged.
3. Integrating with Existing Wellness Programs
We aligned our training solutions with the brewery’s established wellness initiatives, including Fitbit Health at Work, ensuring that employees had complementary resources to improve their physical and mental well-being.
4. Flexible, Employee-Centered Approach
To maximize participation, training was scheduled at optimal times for brewery and remote workers, creating an inclusive and accessible learning environment that encouraged engagement without disrupting operations.

The Results
-
Enhanced Workplace Resilience: Employees gained practical tools to manage stress, balance workloads, and maintain performance under pressure, whether in the brewery or in the office.
-
Stronger Employee Engagement: Custom training aligned with employee needs resulted in higher participation and engagement across teams.
-
Enhanced Corporate Culture: The brewery reinforced its commitment to employee well-being, strengthening its reputation as a top employer and Great Place to Work.
-
Lower Burnout & Health-Related Risks: Addressing key stressors helped reduce absenteeism and improve overall workforce well-being and performance.
